Ⅰ.Design of Production Process for Preparing System of Ultra-fine Powder Production Line
After cleaning, the high-quality and high-whiteness calcite raw materials, which were crushed and screened, were subjected to secondary crushing, and the particle size of the crushed calcite was less than 3-6 mm. Then the hoist is fed into the feeding bin, and the raw material is fed into the high-fine ball mill for grinding by metering. The grinding powder is fed into the hoist by air separation. Under the action of pneumatic suction, the powder is classified into the classifier for particle size classification. The product fineness is 600-3000 mesh and can be adjusted arbitrarily. The qualified fine powder is carried into the special high-pressure pulse bag dust collector by air flow, and the finished product is collected and sent to the storage. The coarse powder separated from the classifier is then sent to the ball mill for grinding. The whole system forms a closed-circuit cycle processing system.
If the product fineness needs to be improved, the separation process steps can be increased many times to produce products with higher fineness.
The production system is operated under negative pressure, and dust collectors are set at dust-raising points of material conversion to prevent dust-raising.
The system equipment adopts advanced DCS control operation, which can control the operation of the whole production system in the central control room and improve the working environment of operators.
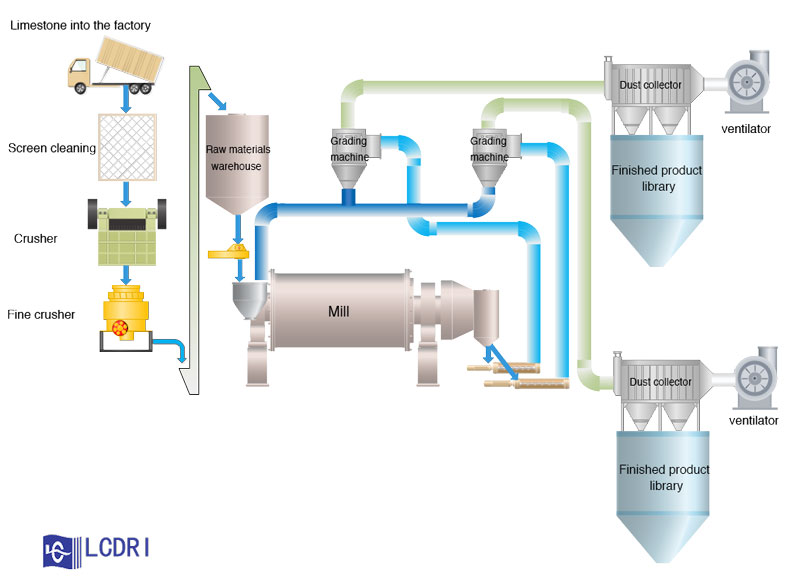
Ultrafine powder grinding system
Ⅱ.Main technical characteristics of the preparation system of ultra-fine powder production line
ⅰ.Dry Ball Milling Technology
- Special design was adopted to optimize the length-diameter ratio of ball mill and improve the grinding efficiency.
- The grinding fineness of the product is improved by using a scientific graded grinding medium.
- Drive bearing adopts rolling bearing + dry oil lubrication mode, which simplifies the lean oil lubrication station and reduces the operation cost.
- The product fineness can reach 3000 meshes by pure dry method.
- Advantages of the product: narrow particle size distribution, continuous and stable batch. Particles are spherical, with large specific surface area, good filling effect and refractive effect, which can meet the requirements of high-end users.
ii.Fine air classification technology
By using multi-level grader and grading process combination, products of different fineness levels are separated to meet the needs of different customers. The classification efficiency of the developed multi-rotor classifier can reach 90%.
The one-time grading fineness can be adjusted in 325-3000 meshes. Adding the secondary classification system can reach the advanced level of dry ultrafine powder classification at home and abroad.
ⅲ.Ultra low emission
The production line layout is compact and reasonable, and the production system operates under negative pressure without dust leakage to meet the emission requirements.
ⅳ.DCS control technology is adopted in production system
The whole production system adopts one-key DCS central control system to realize intelligent production process control from crushing, grinding, grading, storage, packaging, loading and transportation, which ensures real-time production monitoring, ensures the continuous stability of the system, the stability and reliability of product quality, and reduces production costs.
Ⅲ.Technical Advantages of Preparing System for Ultrafine Powder Production Line
- High efficiency and energy saving: high grinding and flour separation efficiency, high product fineness;
- The process is smooth and simple: easy maintenance and low operation cost;
- Green environmental protection: dust and noise emission up to standard;
- Continuous stability, excellent quality: product quality is stable, annual continuous operation time can reach 300 days;
- High performance-price ratio: low cost of comprehensive investment;
- High degree of automation: DCS automatic control of production process;
- Advanced technology and equipment: The advanced technology and equipment at home and abroad are adopted, and the equipment is stable and reliable.
Luoyang Building Materials Architectural Design Research Institute (LCDRI) is a state-level high-tech enterprise specializing in industrial equipment research and development and mineral material production technology services. The company has core technology in cement building material production line, fine powder (slag) production line, active lime production line, solid waste treatment, soil (sludge) environmental protection treatment, oil shale comprehensive utilization, sludge comprehensive treatment and so on.