With the acceleration of China’s urbanization process and the rapid development of society and economy, the intensity of sewage treatment has gradually increased, and the sludge generated therefrom has increased dramatically. At the same time, due to the improvement of China’s environmental standards, sludge is in urgent need of advanced treatment.
Common sludge treatment technologies

The sludge treatment technologies mainly include sludge digestion, drying, composting and incineration.
(1) Sludge digestion
Sludge digestion includes aerobic digestion and anaerobic digestion. The purpose of aerobic digestion is to stabilize the sludge, reduce the harm of the sludge to the environment and soil, and reduce the final treatment capacity of the sludge. The sludge digestion method has the advantages of stability and sterilization, low investment, convenient operation and management, low capital construction costs, odorless final product, and low concentration of supernatant at night, so it is particularly suitable for sludge treatment in small and medium-sized sewage plants. The purpose of anaerobic digestion is to reduce sludge volume and stabilize sludge properties.
(2) Drying
The most effective way to reduce weight is to dry. Drying means that a certain amount of heat energy is transferred to the moisture contained in the material in a unit time. These moisture are vaporized after being heated, separated from the material, and the material that has lost the moisture is vaporized. The moisture content is collected separately, which is the drying process. Sludge drying can reduce the water content from 70% to less than 10%. In fact, according to the needs of final disposal, the final solids content of sludge can vary between 60% and 95%. At this time, the reduction of sludge exceeds 60%, which is more reasonable in terms of cost and safety.
Drying is divided into direct and indirect heating methods, mainly due to the difference in the form of heat source utilization, specifically, directly as a medium or indirectly heating the heat-exchanging medium. Drying is accomplished by heat, which is generally generated by energy combustion.
(3) Sludge compost
Sludge composting is a process of aerobic fermentation using aerobic microorganisms in sludge. It is a self-generating process that can eliminate pathogens and produce a substance similar to humus. Generally, it can be divided into separate compost , Sludge and garbage mixed compost.
(4) Sludge incineration
Sludge incineration can destroy all organic matter, kill all pathogens, and minimize the volume of sludge. The sludge with a relative water content of incineration residue of about 75% is only about 10% of the original volume. When the combustion heat value of the sludge itself is high, the urban sanitary requirements are high, the land is tight, or the sludge has a high content of toxic substances and cannot be comprehensively used, it can be treated by incineration. Before the sludge is incinerated, it should generally be dehydrated and thermally dried to reduce the load and energy consumption. Sludge incineration is technically feasible and has reached an industrial scale.
The characteristics of incineration treatment: greatly reduce the volume and weight of sludge; kill all pathogens; the sludge treatment speed is fast and does not require long-term storage; energy can be recovered. But on the other hand, its higher operating costs and flue gas treatment issues have become the main factors restricting the sludge incineration process.
Common sludge disposal technology
The sludge disposal technologies mainly include resource utilization such as landfill, land use and building materials.
(1) Sanitary landfill of sludge
The sanitary landfill of sludge began in the 1960s. It is based on traditional landfills after scientific site selection and necessary site protection treatment. It has a strict management system and scientific engineering operation methods. Landfill is a relatively mature disposal technology, which has the advantages of simple disposal method, large processing capacity, quick results, easy operation, low cost, no need for high dehydration, and strong adaptability. However, the large land area occupied by sludge landfills has caused most landfill sites to be reluctant to accept sludge under the current shortage of urban land. In addition, there are problems with the management system and management departments cannot clearly distinguish responsibilities. Therefore, the prospect of sludge sanitary landfill is not optimistic.
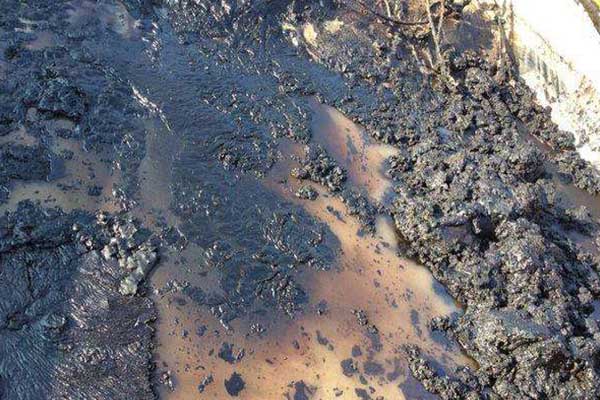
(2) Use of sludge land
At present, the land use types of sludge are many and extensive, such as agricultural and forestry arable land, animal husbandry grassland, garden green land and so on. Land use of sludge refers to the use of soil’s self-purification ability to harmlessly treat sludge. The effective components of sludge can improve soil structure and promote plant growth. It is a better soil improver. This method of disposal is the application of sludge to farmland, municipal greening, nursery substrates and land restoration and reconstruction and replacement of landfill clay. However, considering the heavy metals and harmful substances contained in the sludge itself, and the inadequate acceptance of sludge products by farmers and consumers, and incomplete national relevant policies and norms and standards, domestic sludge farming has struggled.
(3) Comprehensive utilization of building materials
The use of sludge to produce building materials can realize the full use of resources and energy, and can also decompose or solidify the toxic and harmful substances therein. The resource utilization of sludge manufacturing construction materials has significant advantages, and it will be one of the important development directions of sludge resource technology. The building material industry has a very large demand for raw materials, which can absorb a large amount of sludge on site, and has broad application prospects. The currently known methods for building sludge from sludge include bricks from sludge, cement from sludge production, and lightweight ceramsite materials from sludge.
Status and development trend of sludge treatment and disposal

Most of the sludge from urban sewage treatment plants is disposed of in landfills. Some of them are professional landfills, and some are mixed with municipal waste. A small part is disposed of for agricultural use, including returning to the field after stabilization and returning to the field after composting. There is also a part for incineration. The sludge volume of point source facilities in enterprises is relatively small, and the cost of disposal is relatively high. Basically, the enterprise disposes it by itself. According to the nature of sludge, there are various disposal methods.
Development trend
With the continuous progress of environmental protection science and technology, China’s sludge treatment and disposal technology will gradually catch up with the international development trend of sludge disposal, from landfill to incineration disposal, land use, building material use and other comprehensive utilization methods. .
With the increase of urban sewage discharge and treatment rate in China, sludge production has increased significantly, and sludge treatment and disposal are facing new challenges. Therefore, it is urgent to seek solutions based on China’s national conditions and sludge characteristics. The sludge should be turned into a usable substance under the principle of “reduction, stabilization, harmlessness, and recycling” to realize resource recycling and promote the development of circular economy. With the country’s increasing emphasis on environmental protection and increased investment, the technology for sludge treatment and disposal will surely be further developed and improved.