Ⅰ.DISEÑO del proceso de PRODUCCIÓN del sistema de PREPARACIÓN PARA LA FABRICACIÓN de micropolvos superfinos
La materia prima de un antídoto fino de gran calidad,blanco y triturado después de la limpieza,entróen la segunda rotura y el tamaño de la partícula se fracturóen<3 a 6 mm.Posteriormente,los ascensores los introducen en el depósito de alimentación,donde se calcula que los materiales se alimentan con molinos de molienda de bolas de alto nivel.Los polvos finos se introducen en las máquinas de elevación por selección de viento,y los polvos entran en las máquinas de clasificación por tamaño de partícula por efecto de succión de la fuerza del aire,con un grado de detalle de 600 a 3.000 renglones que pueden adaptarse de cualquier manera.Los polvos finos calificados se introducen por la corriente de aire en un colector especial de sacos de impulsos de alta presión,que recoge los productos acabados y los envía a un depósito; los polvos en bruto separados por la cascada se envían luego al molino de bola para su molienda.Todo el sistema forma un sistema de ciclo cerrado.
Si es necesario aumentar el nivel de detalle de los productos,se pueden añadir varias etapas del proceso para producir productos más detallados.
El sistema de producción funciona a presión negativa,y los puntos de precipitación para la conversión de materiales establecen receptores contra el polvo.
El equipo del sistema utiliza operaciones avanzadas de control DCS que permiten controlar el funcionamiento de todo el sistema de producción en la Sala de control central y mejorar el entorno de trabajo de los operadores.
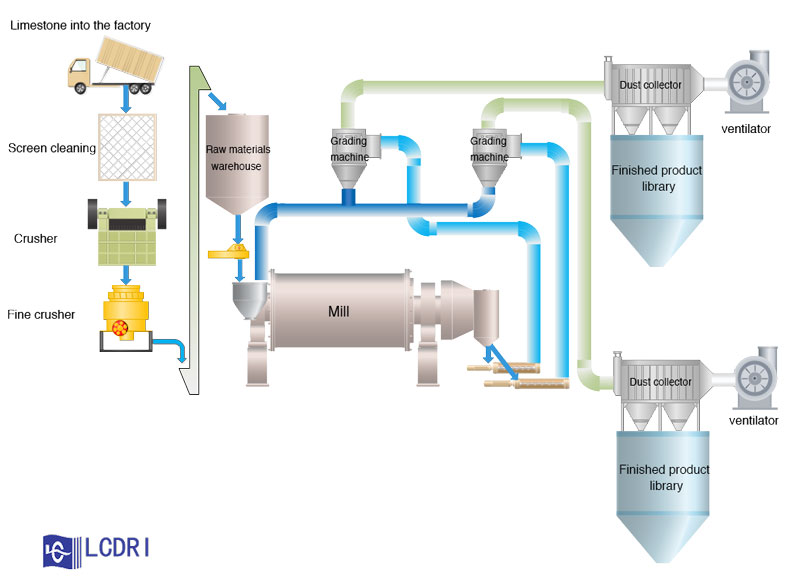
Ultrafine powder grinding system
Ⅱ.Principales características TÉCNICAS de los sistemas de PREPARACIÓN de la cadena de PRODUCCIÓN DE micropolvos superfinos
ⅰ.molienda en seco
1.Optimización de la relación longitudinal del molino mediante diseño especial,aumentando la eficiencia del molino de polvo.
2.Los medios de molienda en cascada científica han aumentado el nivel de molienda de los productos.
3.Los cojinetes de transmisión se utilizan como cojinetes de desplazamiento+lubricantes secos,lo que reduce los gastos de funcionamiento de las estaciones de lubricantes diluidos.
4.Producción pura en seco con un nivel de detalle de 3.000 productos.
5.Ventajas del producto:distribución estrecha de las partículas y estabilidad continua del volumen.Las partículas están en forma esférica,son más grandes que los cuadros,mejor relleno,mejor refracción,pueden satisfacer las necesidades de los usuarios de alto nivel.
ii.técnicas de clasificación de corrientes gaseosas
Utilizando una combinación de procesos graduales y graduales de varios niveles,se separan productos de varios niveles de detalle para satisfacer las necesidades de los distintos clientes.La eficiencia de clasificación de las subestaciones múltiples desarrolladas puede alcanzar el 90%.
Los detalles de la clasificaciónúnica pueden ajustarse entre 325 y 3.000 renglones.Añadir un sistema de clasificación secundaria hasta el nivel avanzado de clasificación de polvos finos finos,tanto nacionales como extranjeros.
ⅲ.Emisiones muy bajas
Funcionamiento del sistema de producción a presión negativa,sin fugas de polvo,para cumplir los requisitos de emisión.
ⅳ.Sistemas de producción
El conjunto de sistemas de producción se basa en un sistema central de control del DCS(DCS),que permite un control inteligente del proceso de producción a partir de la fragmentación,el molienda,la clasificación,el almacenamiento,el embalaje y el embarque de todo el proceso,garantiza el control en tiempo real de la producción,garantiza la estabilidad del sistema,la estabilidad de la calidad del producto y reduce los costos de producción.
Ⅲ.Ventajas técnicas del sistema de preparación de la línea de producción
1.Eficiencia energética:alta eficiencia en la molienda de polvo y gran detalle del producto;
2.Fluidez del proceso:facilidad de mantenimiento y bajo costo de explotación;
3.Protección del medio ambiente:cumplimiento de las normas sobre emisiones acústicas de polvo;
4.Estabilidad continua,alta calidad:estabilidad de la calidad del producto,hasta 300 días de funcionamiento continuo al año;
5.Relación costo-calidad:bajo costo de la inversión combinada;
6.Alto grado de automatización:control automático del proceso de producción DCS;
7.Equipo de alta tecnología:estable y fiable con equipo de alta tecnología nacional e internacional.
El Instituto de arquitectura de materiales de construcción de Luoyang(lcdri)es una empresa nacional de alta tecnología especializada en investigación y desarrollo de equipo industrial y servicios técnicos para la producción de materiales minerales.La empresa cuenta con tecnologías básicas en las líneas de producción de materiales de construcción de cemento,las líneas de producción de polvo(escorias),las líneas de producción de cal activa,el tratamiento de residuos sólidos,el tratamiento ambientalmente racional del suelo(fangos cloacales),el uso integrado de esquistos oleosos y el tratamiento integrado de fangos oleosos.